
CATEGORY
CONTACT US
JI FEI HOLDING LIMITED
Contact person:Jennifer.Ben
Mobile:0086-13968786644
Email: info@vibrationmotor.net
Skype:jfservice
What’s the difference between a Brushless Motor and a Brush Motor?
Well, the brushes of course.
Yeah, but what does that mean?
The principle behind the internal working of both a brushless DC motor and a brushed DC motor are essentially the same. When the motor windings become energized, a temporary magnetic field is created that repels(and/or attracts) against permanent magnets. This force is converted into shaft rotation, which allows the motor to do work. As the shaft rotates, electric current is routed to different sets of windings, maintaining electromotive repulsion/attraction, forcing the rotor to continually turn.
Construction differences
Brushes inside electric motors are used to deliver current to the motor windings through commutator contacts. Brushless motors have none of these current carrying commutators. The field inside a brushless motor is switched via an amplifier triggered by a commutating device, such as an optical encoder.
Windings are on the rotor (Rotating part of motor) for brush motors and on the stator (stationary part of motor) for brushless motors.
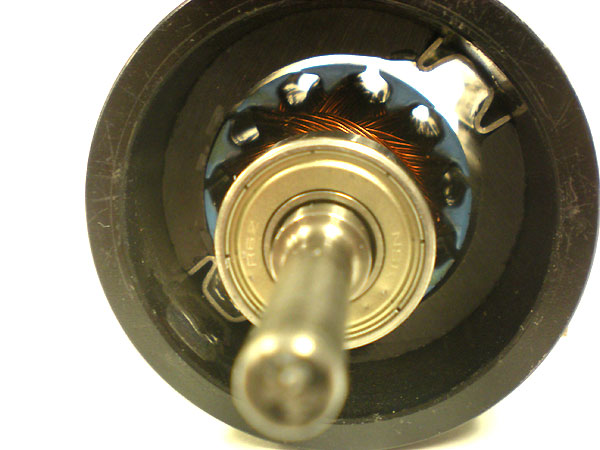
Brush Motor: windings on rotor, magnets on stator
By positioning the windings on the outside stationary portion of the Electric motor the need for brushes can be eliminated.
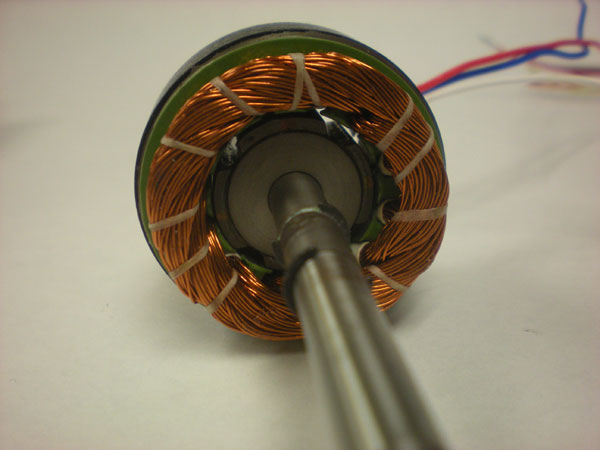
Brushless Motor: Windings on stator, magnets on rotor
There are hints of Brush motors being first developed in the 1830s, by Michael Faraday
Brushed motor Advantages:
Simplified wiring: Brush motors can be wired directly to DC power and control can be a simple as a switch.
Low cost:
Brushed Motor Disadvantages:
Less efficient
Electrically noisy: The switching action of the commutators constantly creating and breaking inductive circuits creates a great deal of electrical and electromagnetic noise.
Lifespan: As they are in perpetual physical contact with the shaft, brushes and commutators wear out.

Showing Brushes and Commutators

Showing Motor Brushes with Rotor removed
Brushless Motor Advantages:
Long lifespan: No brushes to wear out
low maintenance: No brushes to replace
High efficiency
Brushless Motor disadvantages:
High initial cost: Need for commutating device like an encoder and a drive or controller
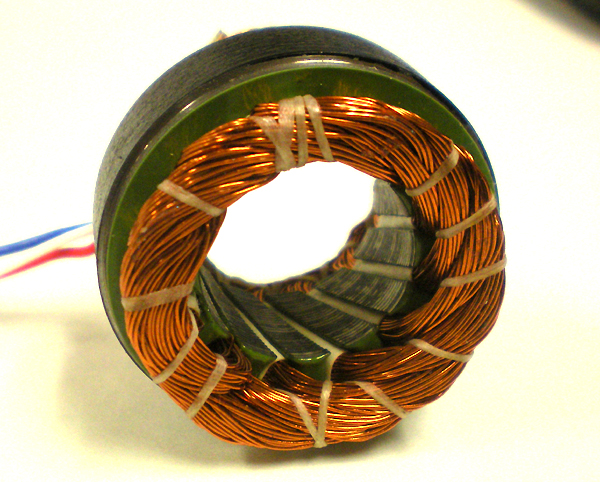
Brushless motor stator
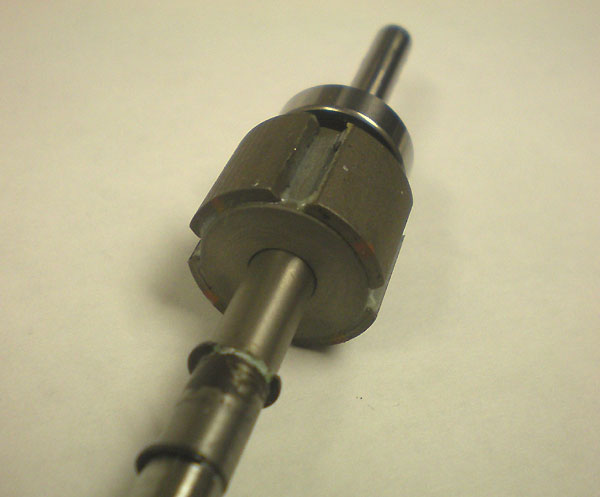
Brushless Motor Rotor
Brusheless motor vs brush motor efficiency:
Brushless motors are typically 85-90% efficient whereas brushed DC motors are around 75-80% efficient.
This difference in efficiency means that more of the total power used by the motor is being turned into rotational force and less is being lost as heat.
with love
www.coin-motor.com
.
Prev article:Vibration Puff and Vibrating DC Motor Next article:1.5v 4mm Micro DC Drive Motor for R/C Train |